The Cloud Bag
*Work in Progress*
*Work in Progress*
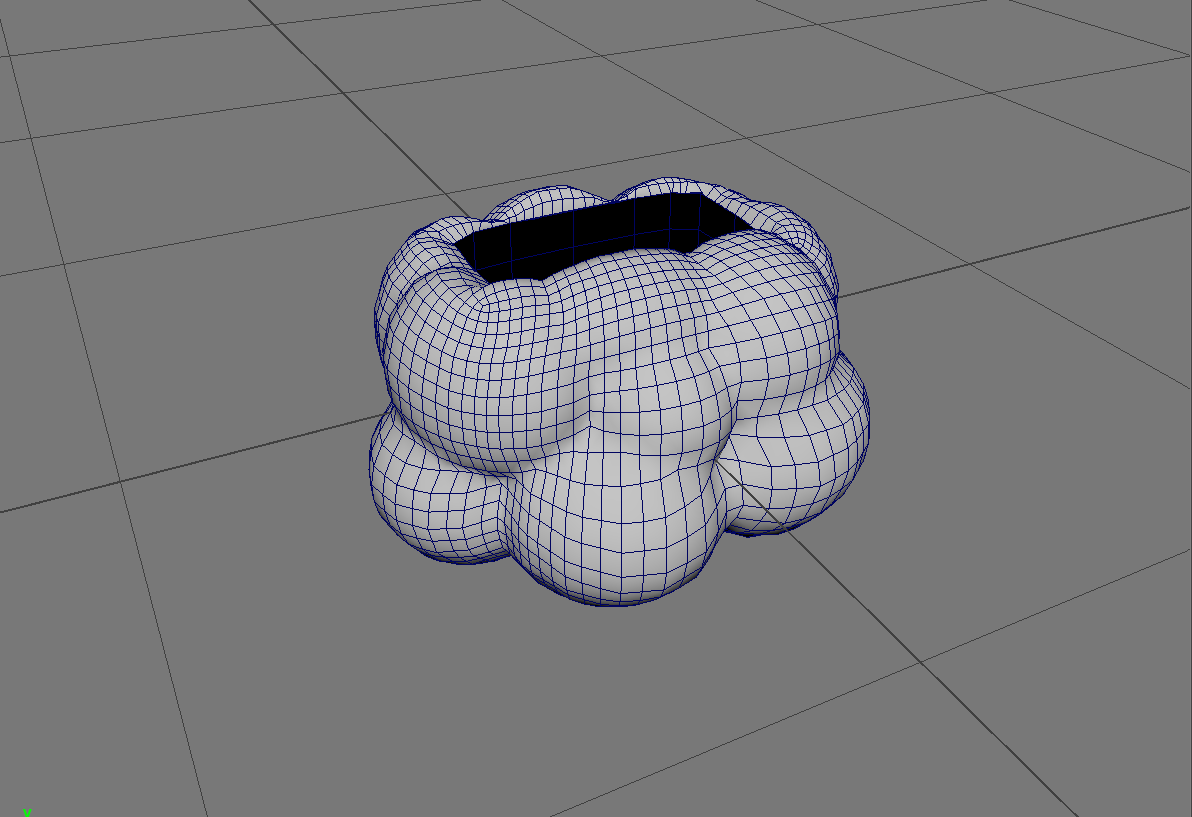
Cloud Wireframe
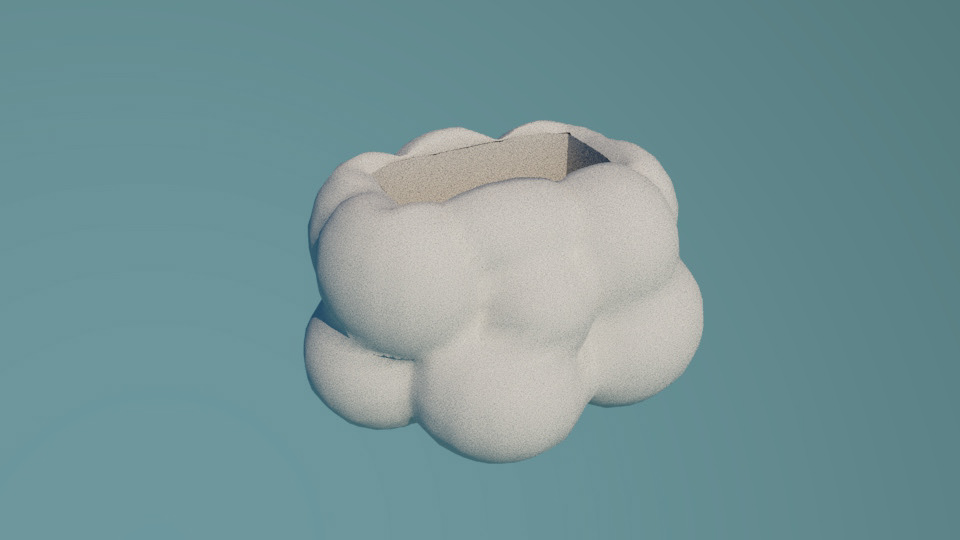
Cloud Render
Softgoods project to develop a small, cute, and cushioned cloud shaped shoulder bag for carrying a camera or personal items. The Cloud Bag is equal parts fashion accessory and padded container.
Please note this project is in the prototyping phase.
Relevant Experience: Rhino 3D, Siemens NX, Mold Design, Sewing, 3D Printing.
The cloud shape and cushioning capabilities of the bag are a result of an unconventional manufacturing process for bags: urethane foam casting. Rather than cushioning the bag with pieces of foam encased in fabric and sewn together, the foam enclosure is cast as one piece. The urethane foam is adhesive while curing, therefore fabrics securely bond to the foam cloud with no additional adhesive applied.
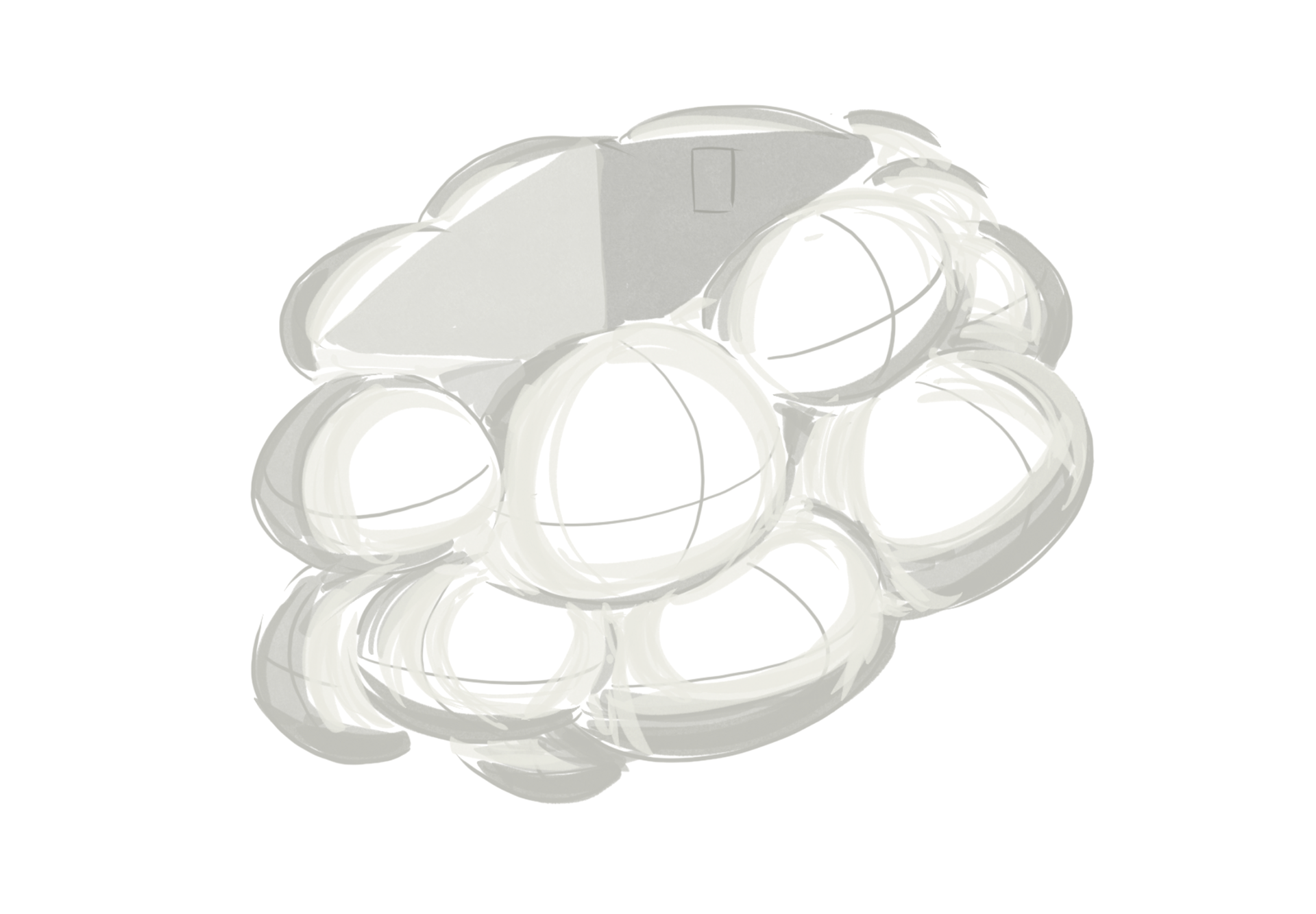
Cloud Exterior Concept Sketch
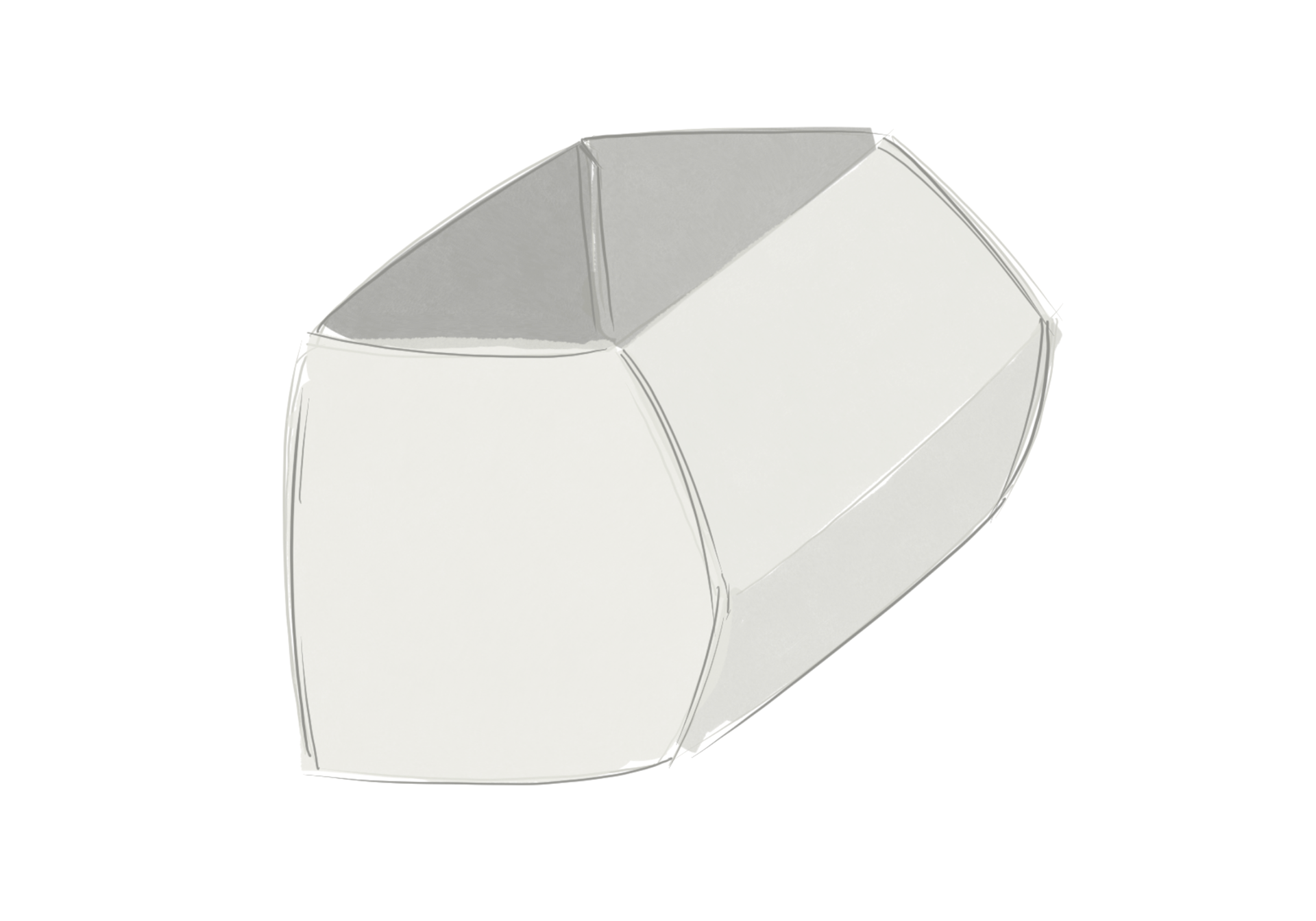
Ripstop Lining Concept Sketch
Bag Exterior: White Polyester Sherpa Fabric. Mimics fluffiness of cloud.
Bag Lining: Ottertex 70D Nylon Ripstop Fabric. Soft touch on cameras and other devices.
Bag Fill: Smooth-On FlexFoam-iT III Urethane Casting Foam.
Exterior Sherpa Fabric
Ripstop Lining
Urethane Foam Casting Tests:
The Polyester Sherpa Fabric and Nylon Ripstop Fabric both successfully bond to the urethane foam forming a single part.
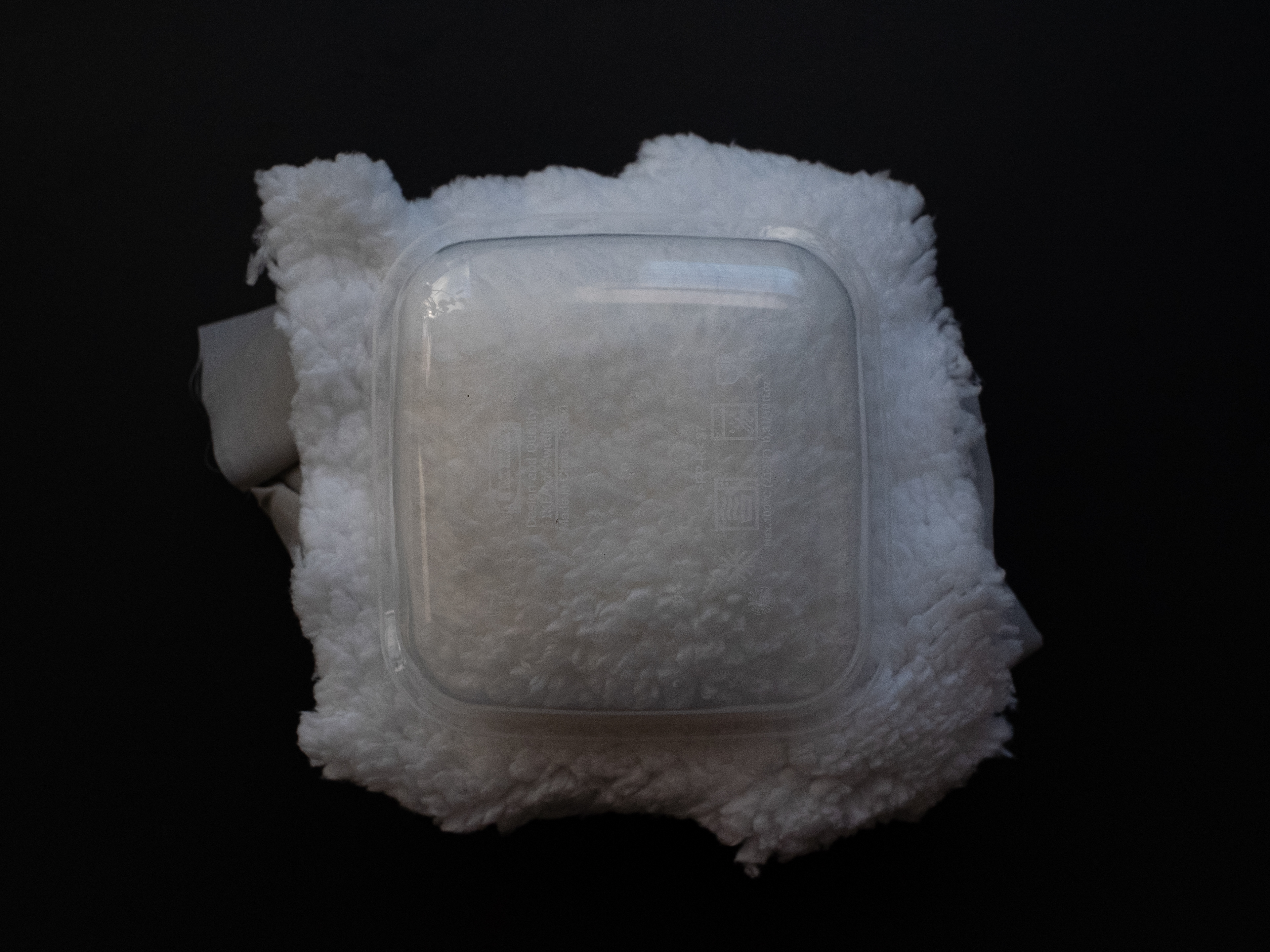
Sherpa Side in the Mold
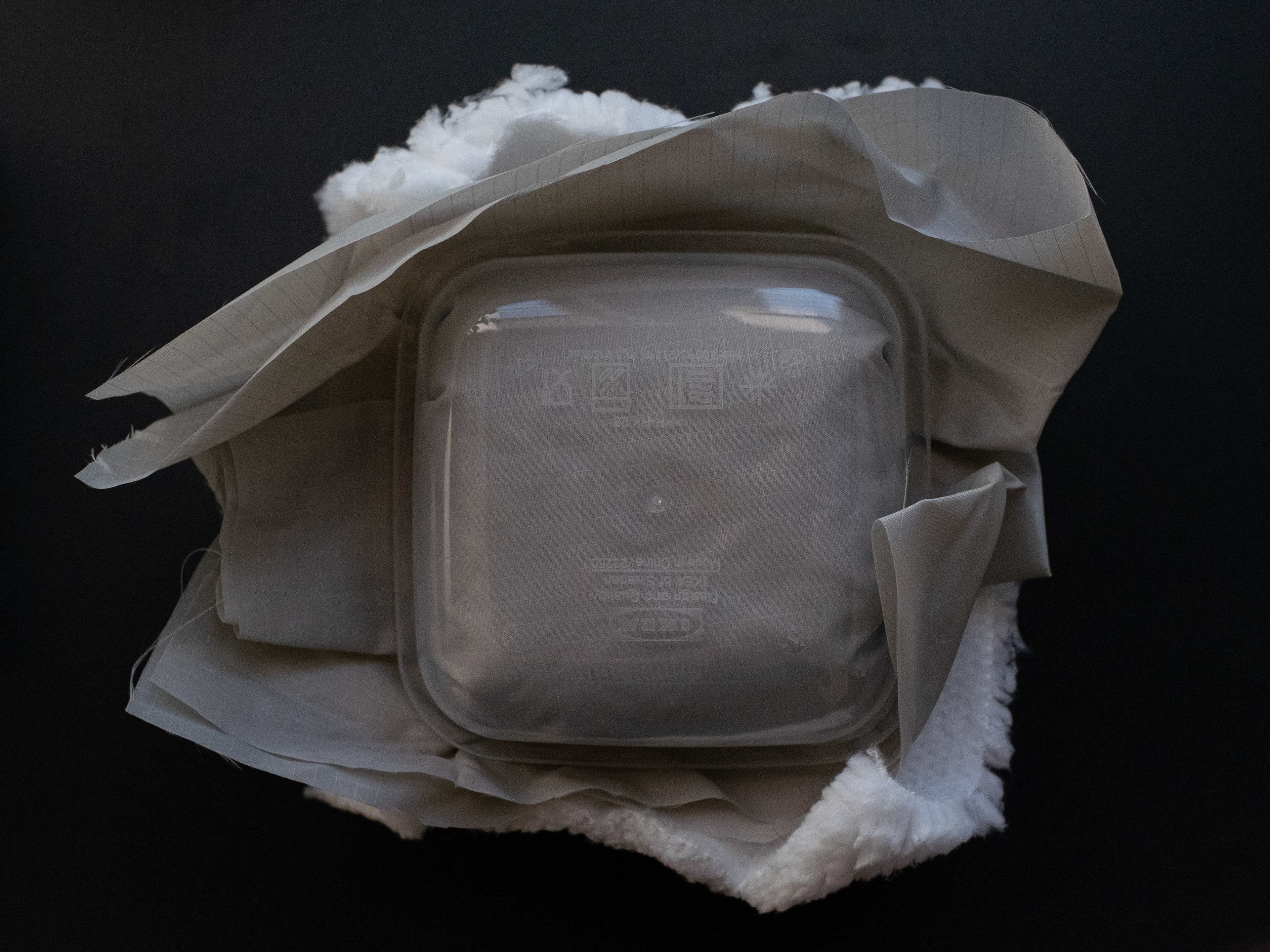
Ripstop Side in the Mold
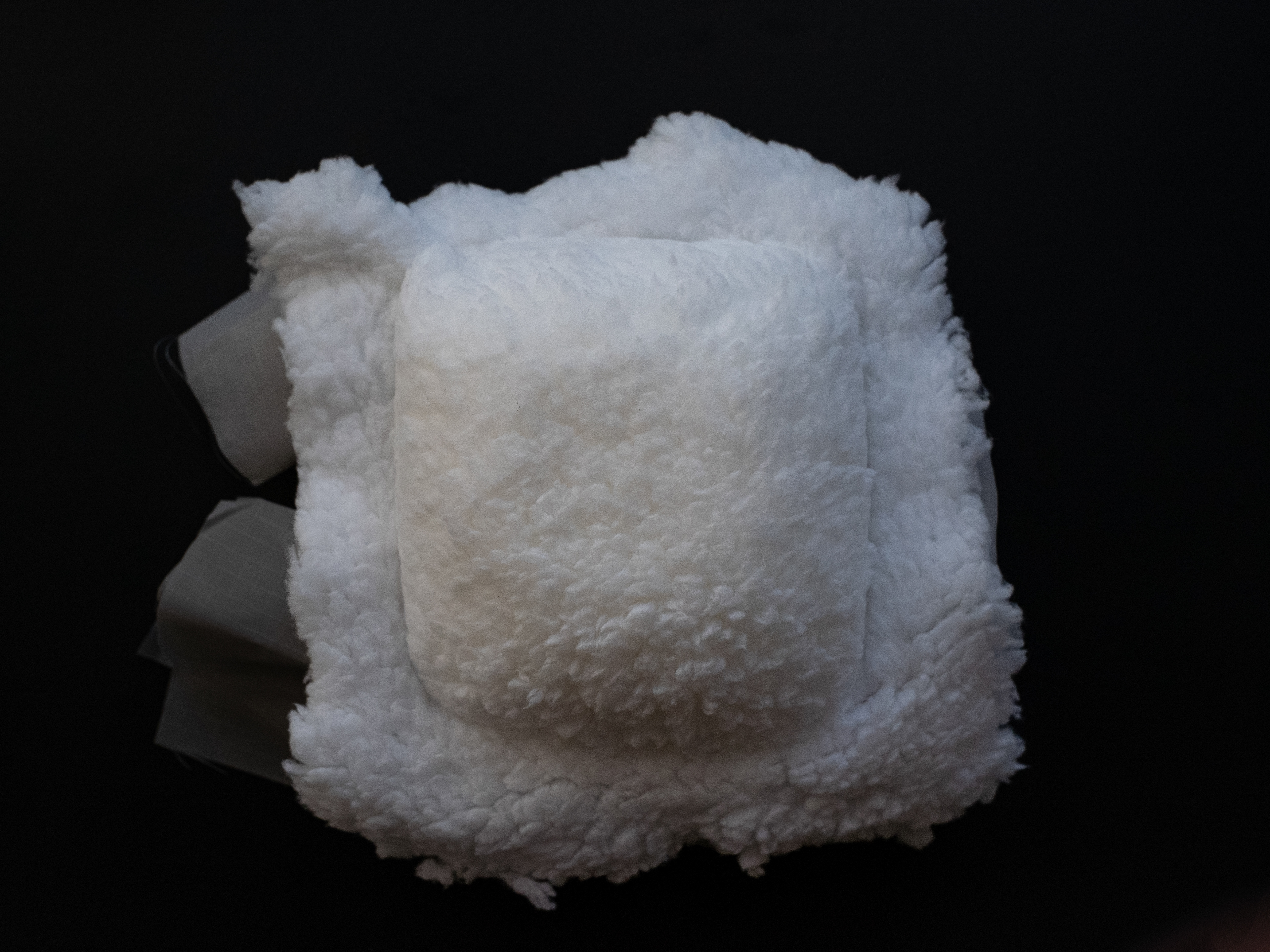
Sherpa Side Removed from the Mold
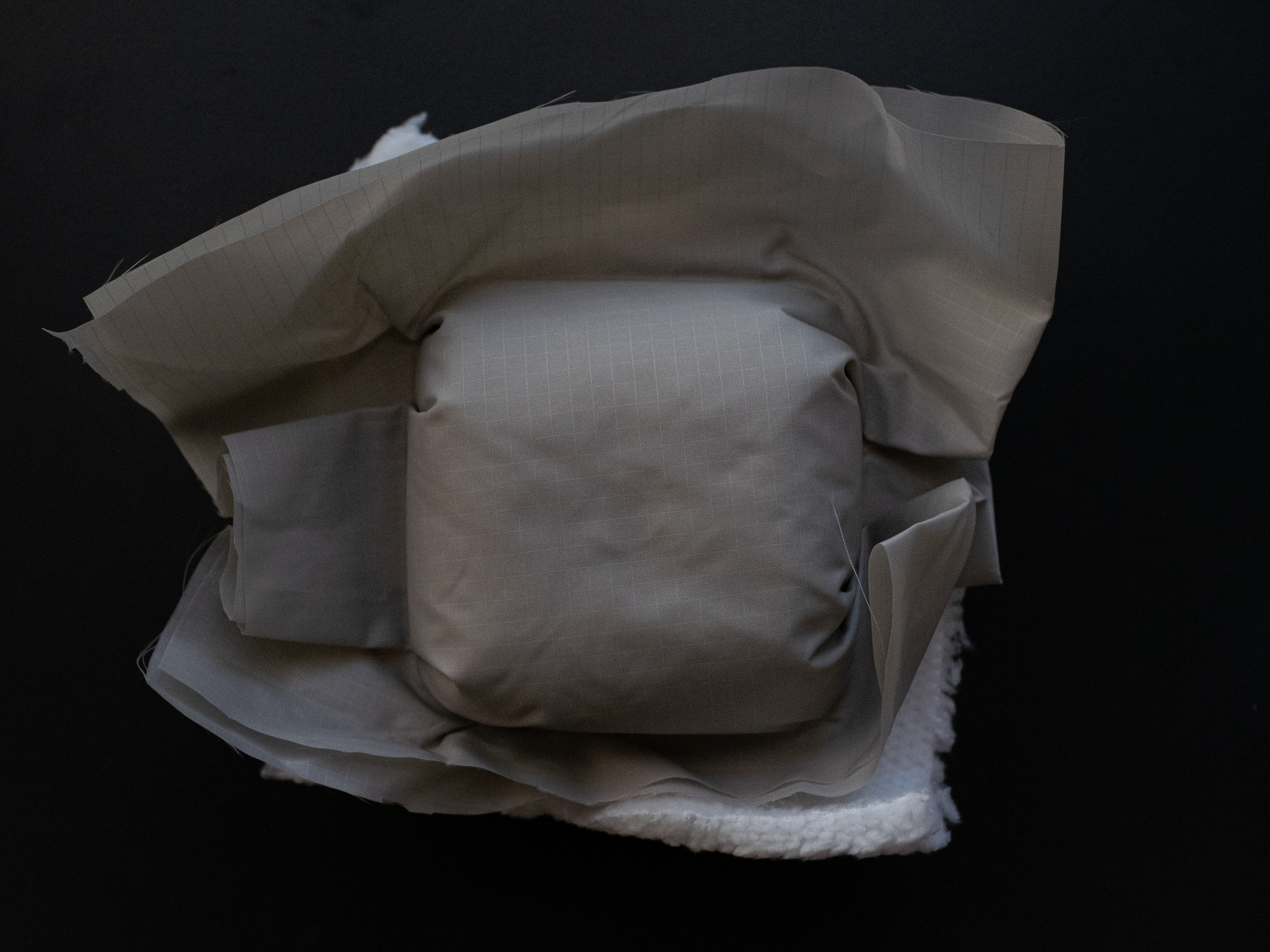
Ripstop Side removed from the Mold
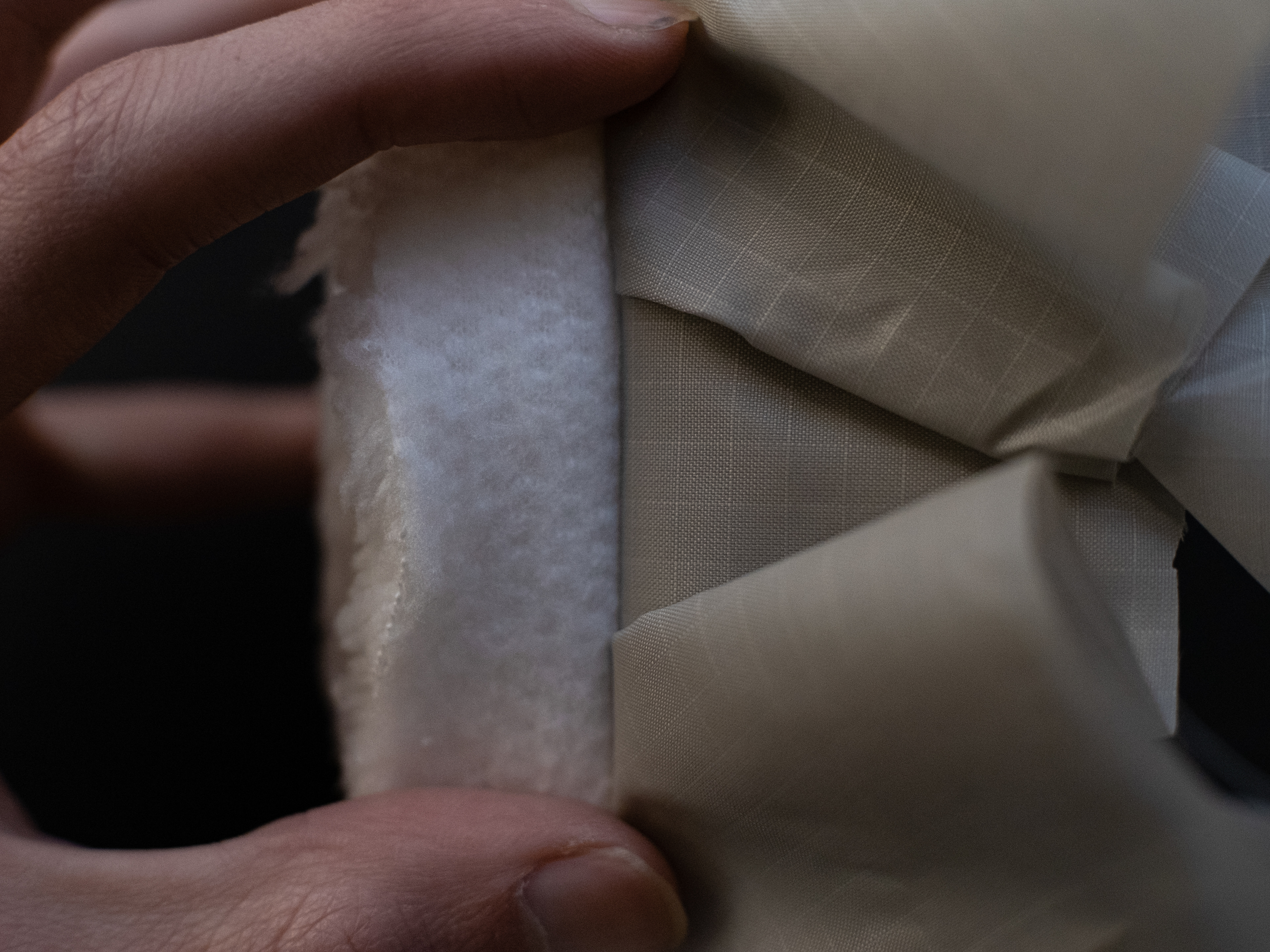
Seam Between Adhered Materials
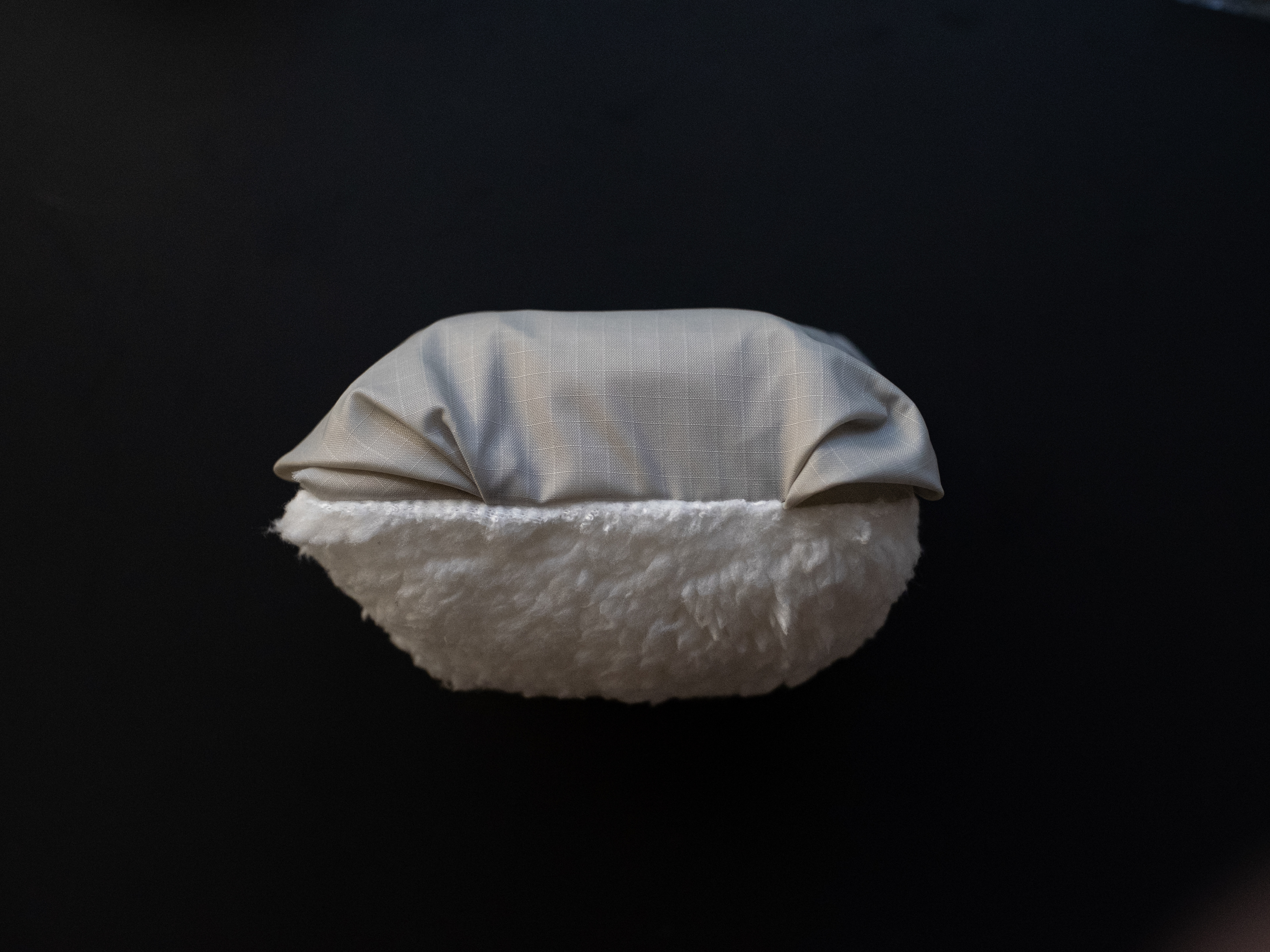
Side View After Trimming
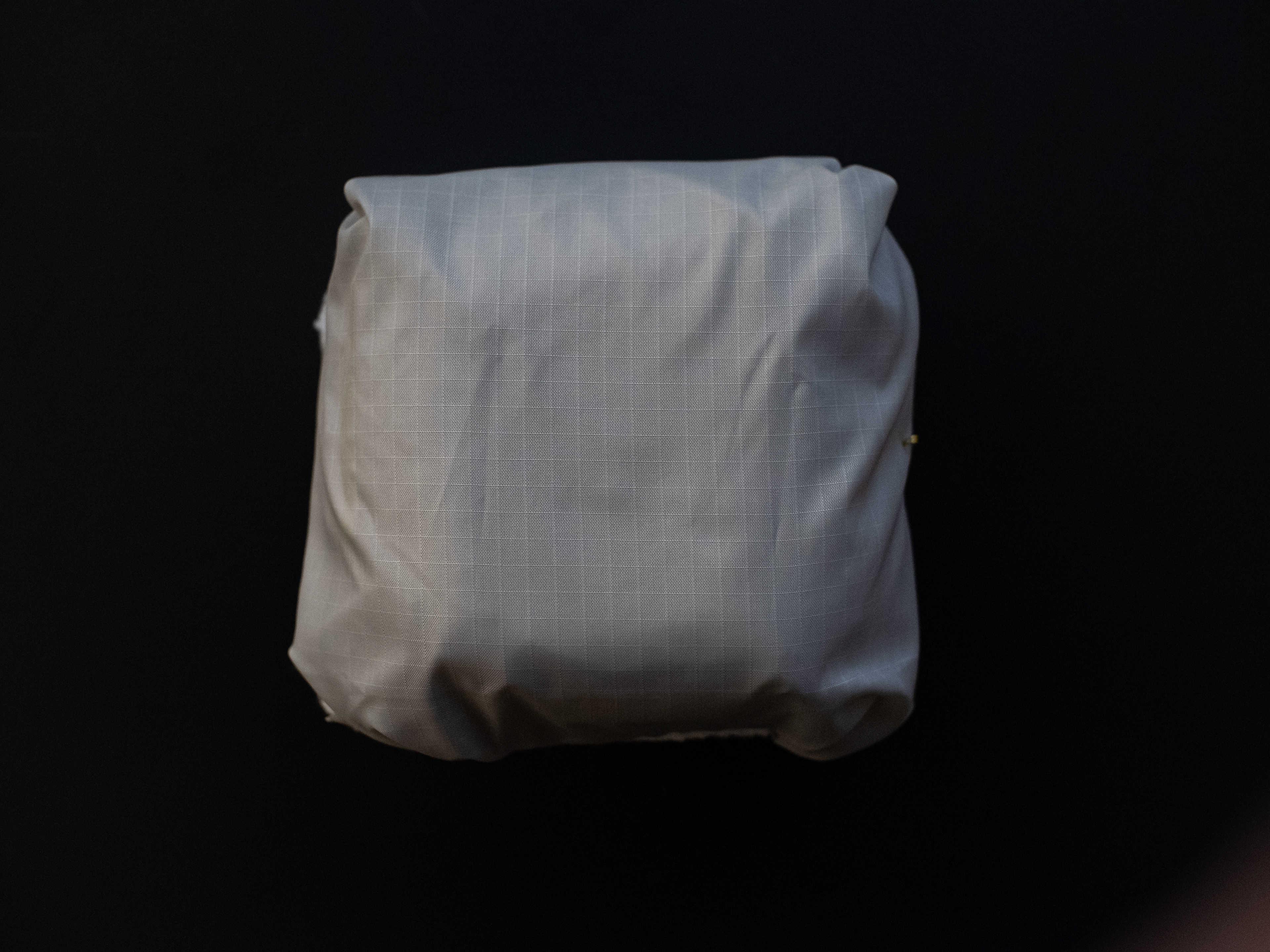
Ripstop After Trimming Excess
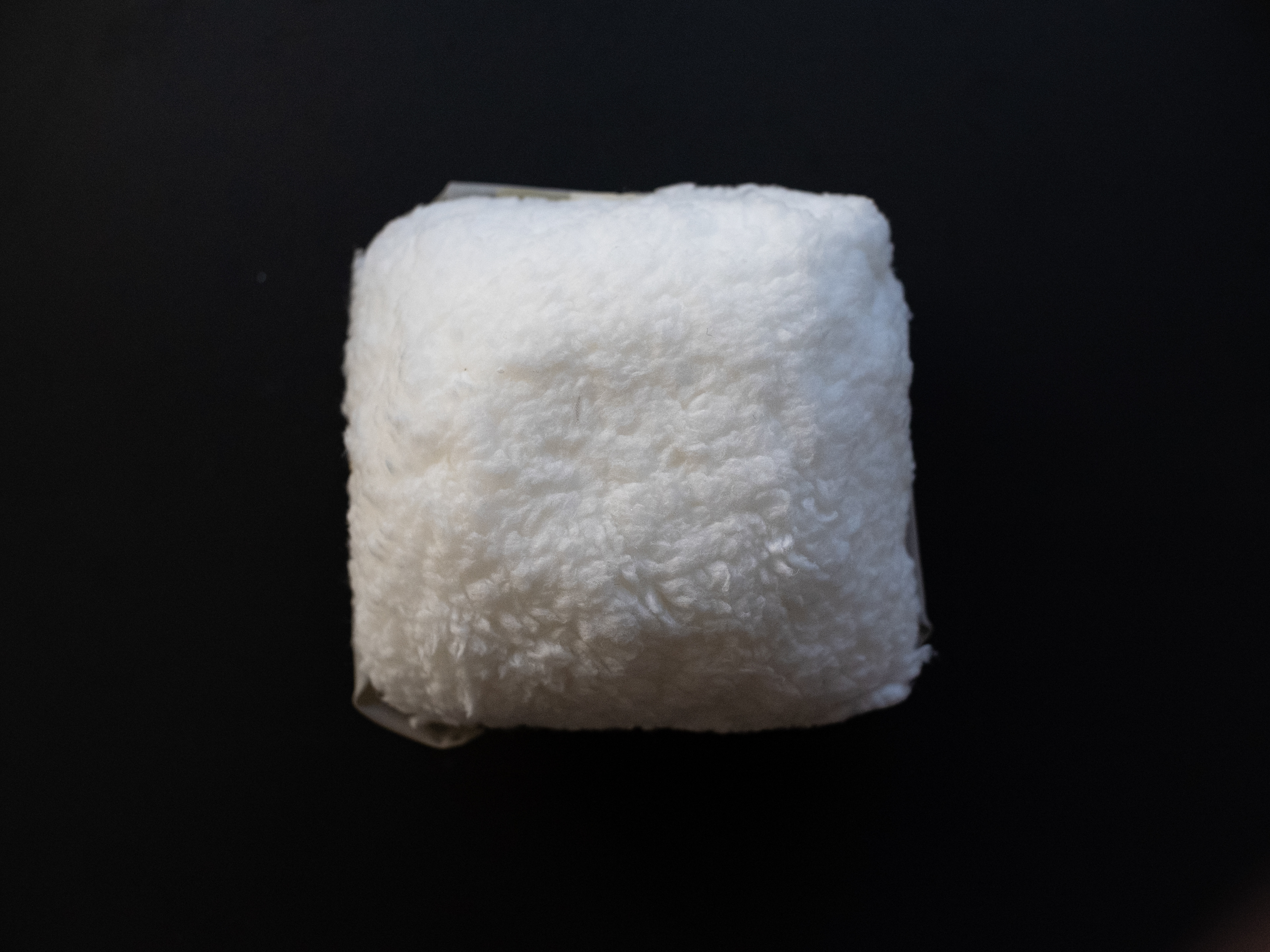
Sherpa After Trimming Excess
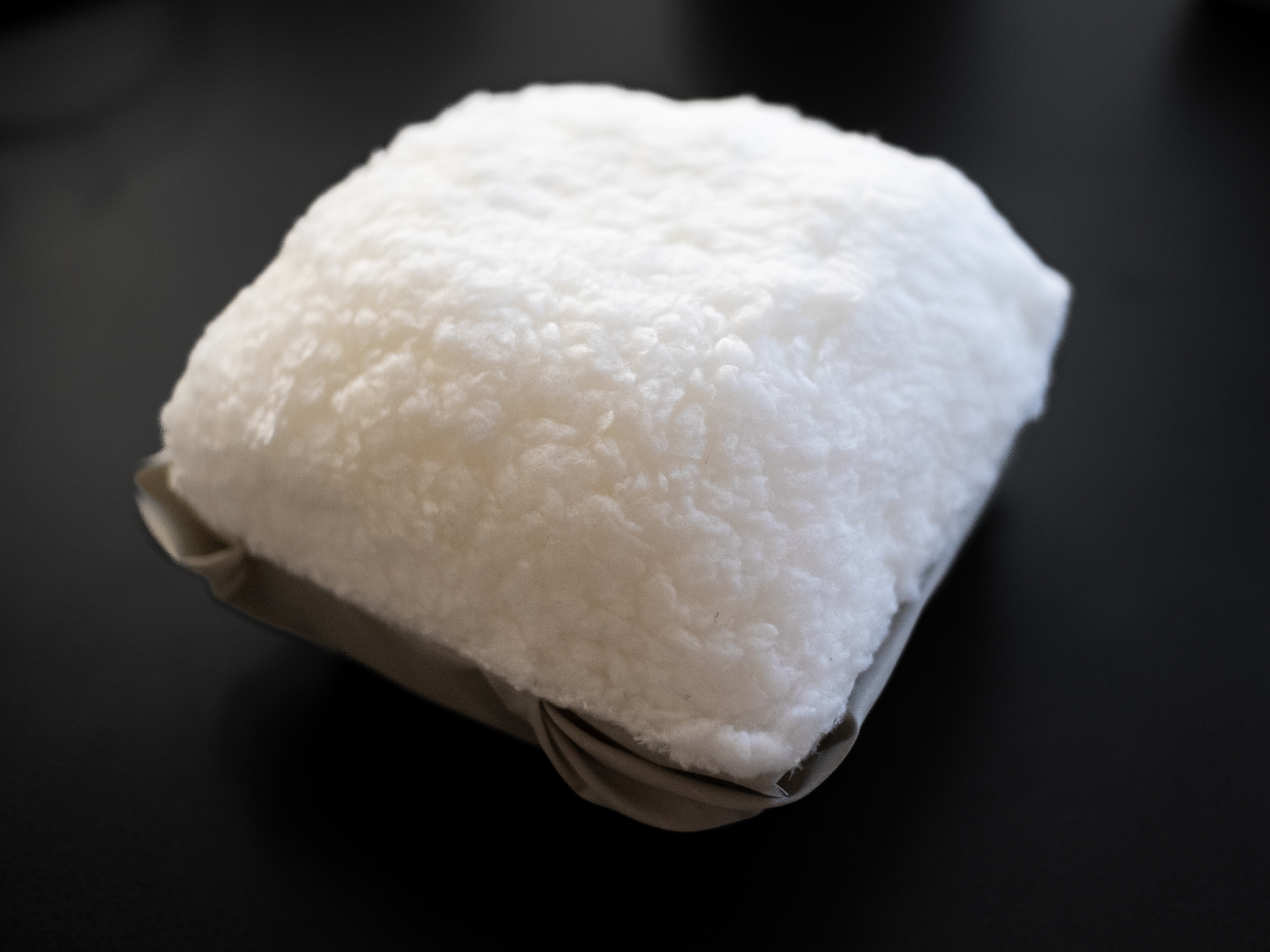
3/4 View After Trimming
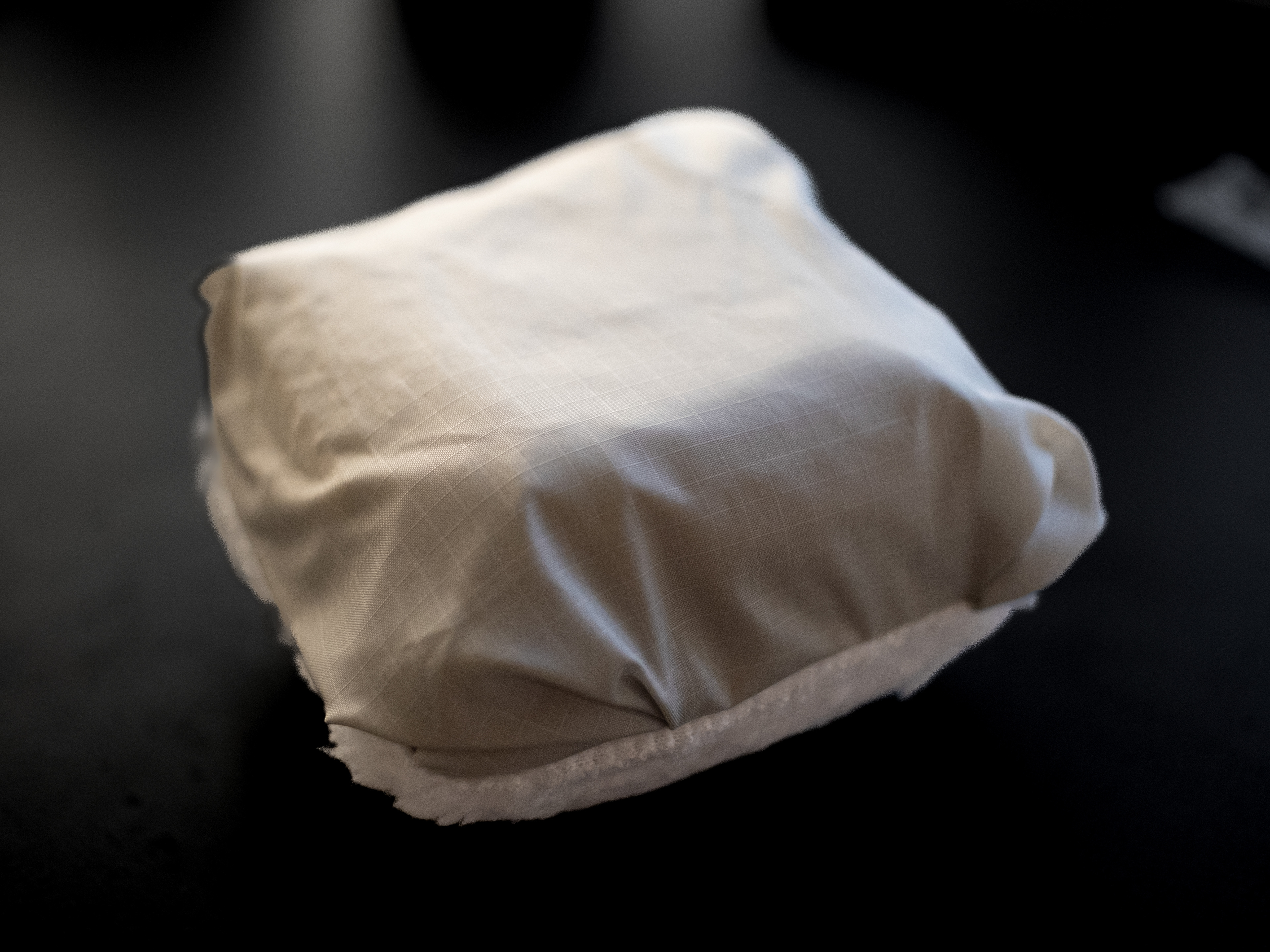
3/4 View After Trimming
Mold Design:
Using NX CAD software, a 3D-printable 3-part mold was designed for the cloud bag prototype (below). After lining the mold cavities with polyester sherpa fabric and the mold core with nylon ripstop, urethane foam is poured in through the opening at the top of the cavities. The foam expands and adheres to the fabrics.
V-grooves and spherical protrusions on each of the mold parts enable exact kinematic constraint to ensure the mold parts achieve the same relative orientation every time they are assembled.
Mold Cavity Detail
3-Part Mold
Full-Scale Foam Cloud Test:
To test the 3D printed mold cavities, a fabric wrapped solid foam cloud was cast. The foam cured for 2 hours before removing from the mold at which point the excess fabric was trimmed from the cloud along the parting line.
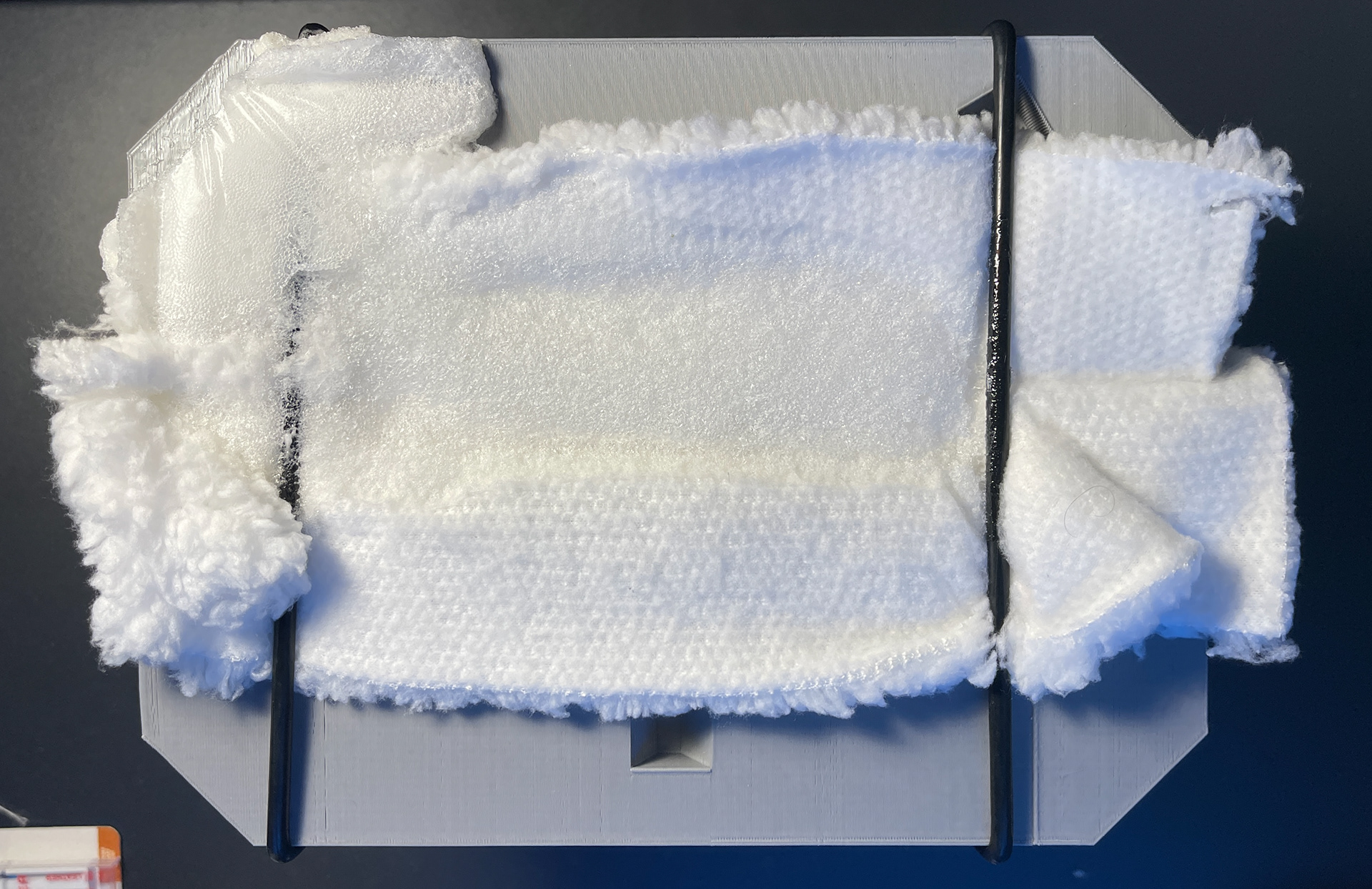
Foam Curing in Mold
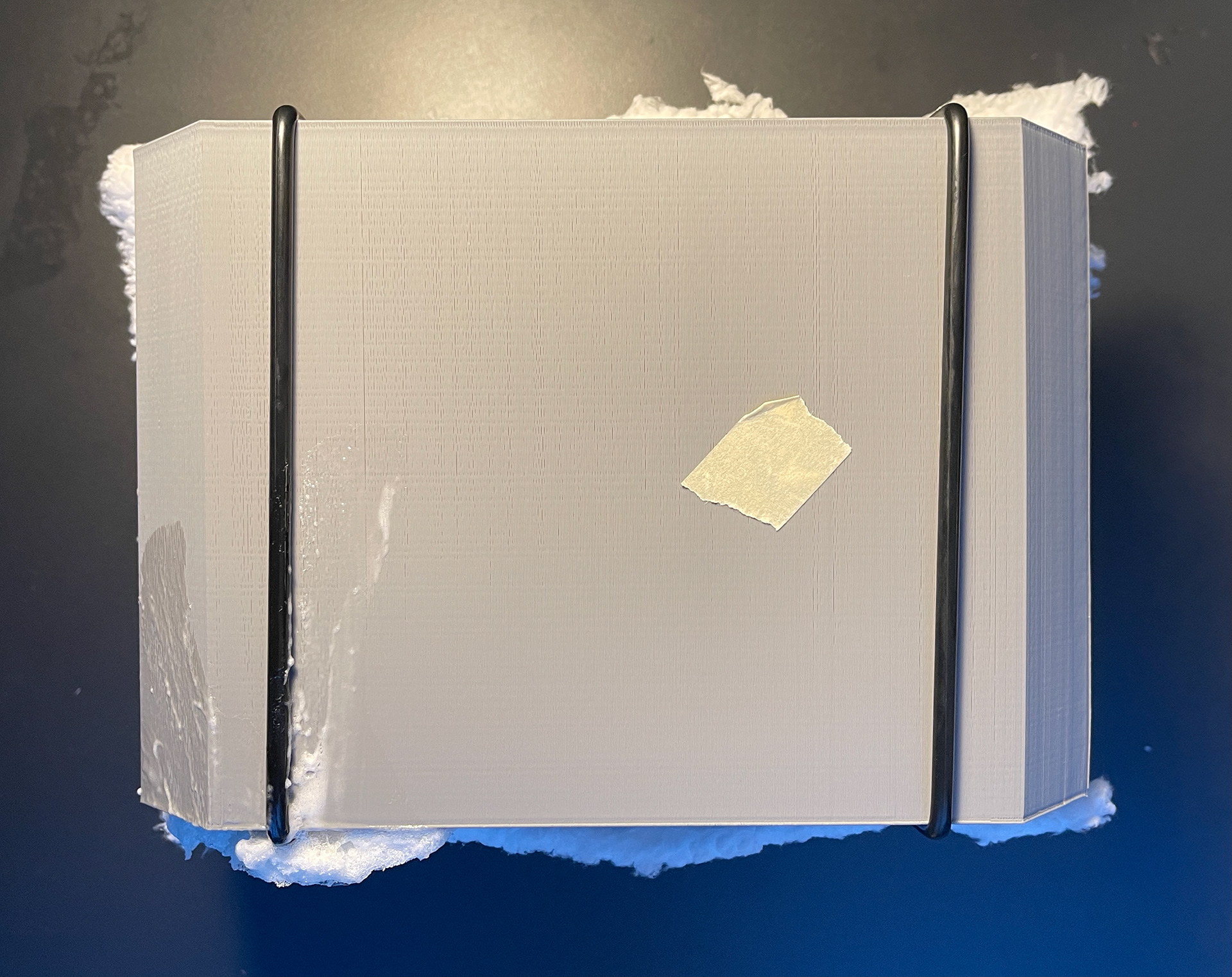
Foam Curing in Mold
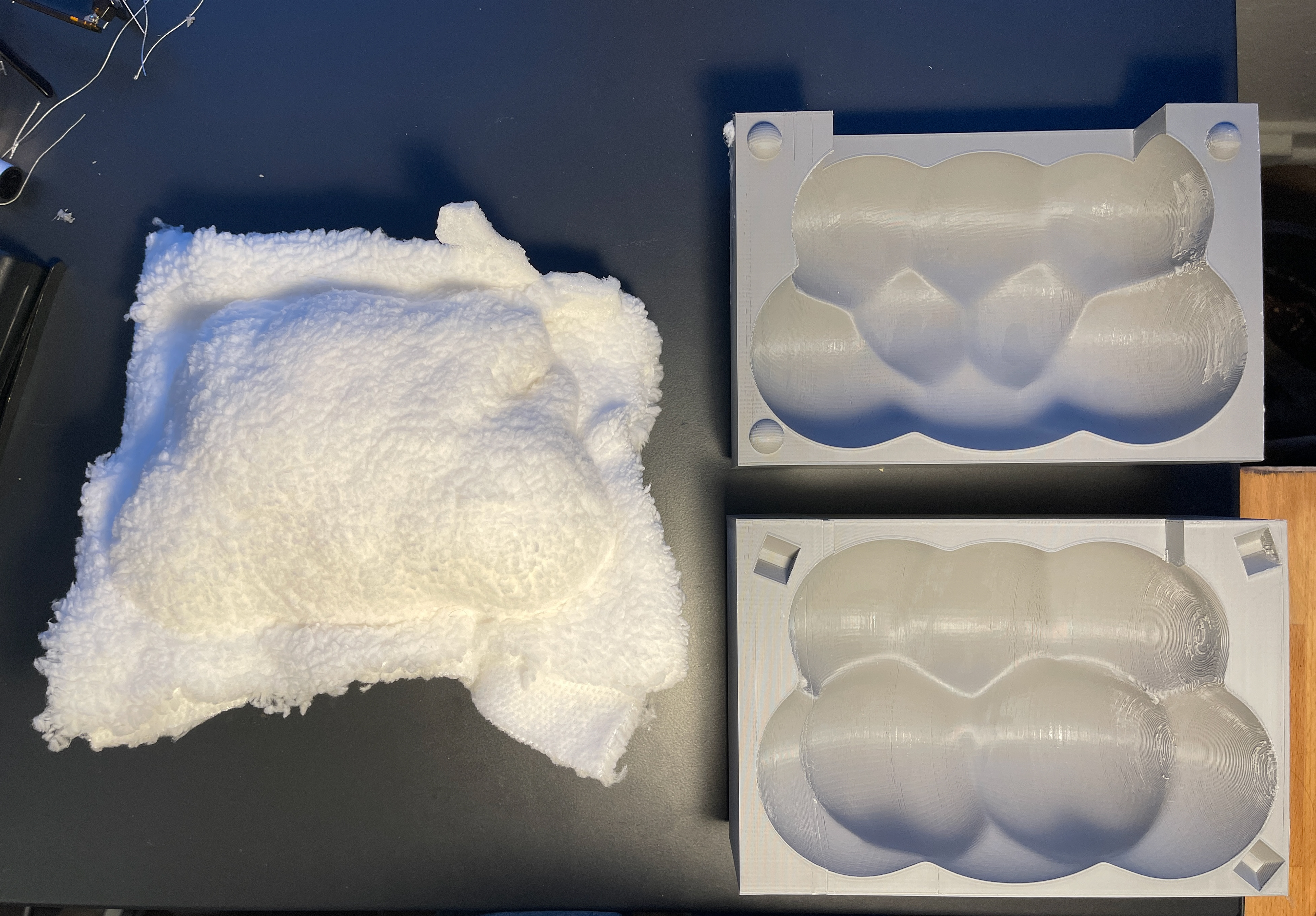
Fabric Covered Foam Removed from 3D Printed Molds
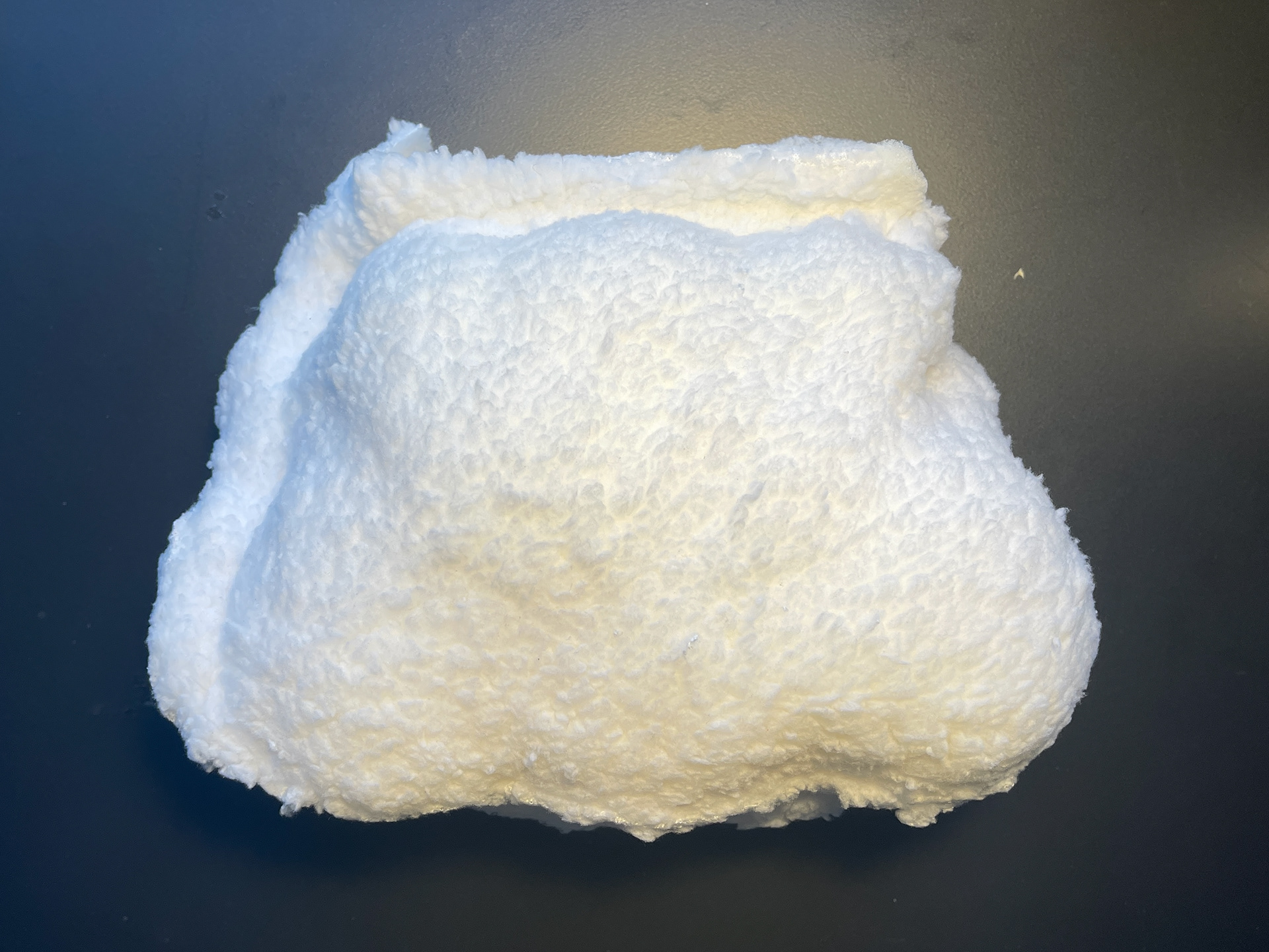
Trimming Excess Fabric
Bag Lining:
Testing ripstop lining sew pattern with 1/4 scale mock-up.